Table Of Content
- The Design-Build Method of Project Delivery Explained
- What Is Design Bid Build In Construction Projects?
- Preliminary Design and Cost Estimation
- What is so different between Design Bid Build and Design Build?
- 702 Forms for use in contracting for architect-engineer services.
- Lack of Owner Control
- Project examples
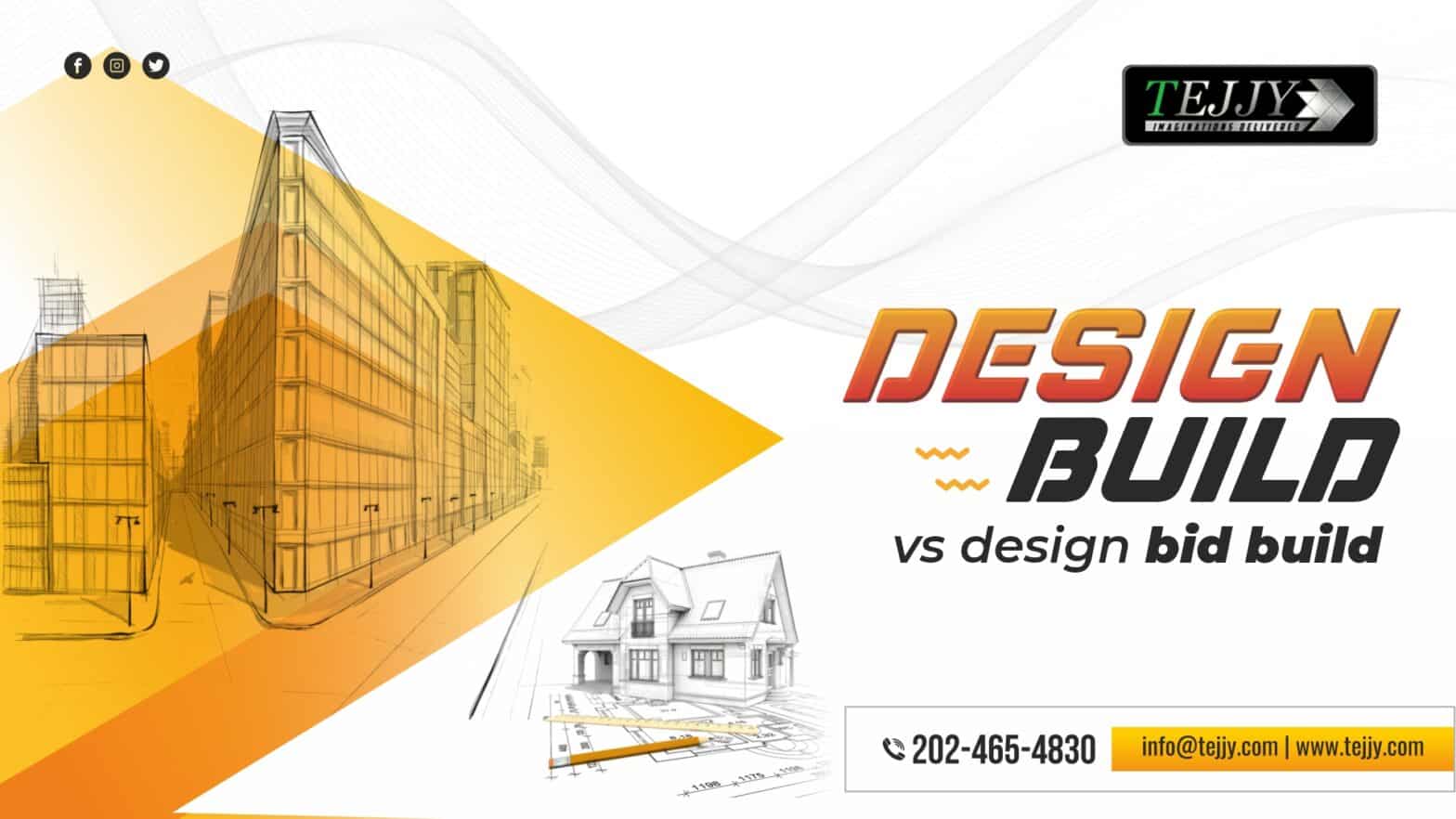
When researchers at FMI first looked at design-build utilization in 2018, the news confirmed what many in the industry knew first-hand, design-build wasn’t an “alternative delivery process” anymore. The latest market analysis forecasting through 2026 shows that is especially true today as impressive design-build growth will continue, despite unprecedented COVID-19, supply chain and labor shortage challenges. It’s the fastest growing and most popular method used to deliver construction projects in America. By integrating subsurface utility mapping into the project delivery process, all stakeholders can set themselves up for a successful project.
The Design-Build Method of Project Delivery Explained
Design builders that understand subsurface conditions can make more competitive bids, streamline the design process, and prevent utility conflicts from causing unnecessary delays. With design build, the design builder can be taking on a much larger or even the entire share of the risk of utility relocation, utility strikes, and delays. They also can be responsible for managing much more of the utility coordination than under a design bid build contract—including both with private utilities, third parties, and other projects in adjacent areas.
What Is Design Bid Build In Construction Projects?
The design-bid-build delivery method is the traditional standard for construction projects and historically the most popular method. For one, the owner contracts with both an architect/engineer for the project’s design and a contractor to construct the project. Then the Owner uses their preferred selection criteria to identify 3–5 of the most qualified bidders to submit technical proposals. This competitive selection process is just one reason why Owners are more likely to report high-satisfaction with design-build projects. Owner preferences and abilities, locales, and project times may impact the top priorities for the project delivery teams that work on them.
Preliminary Design and Cost Estimation
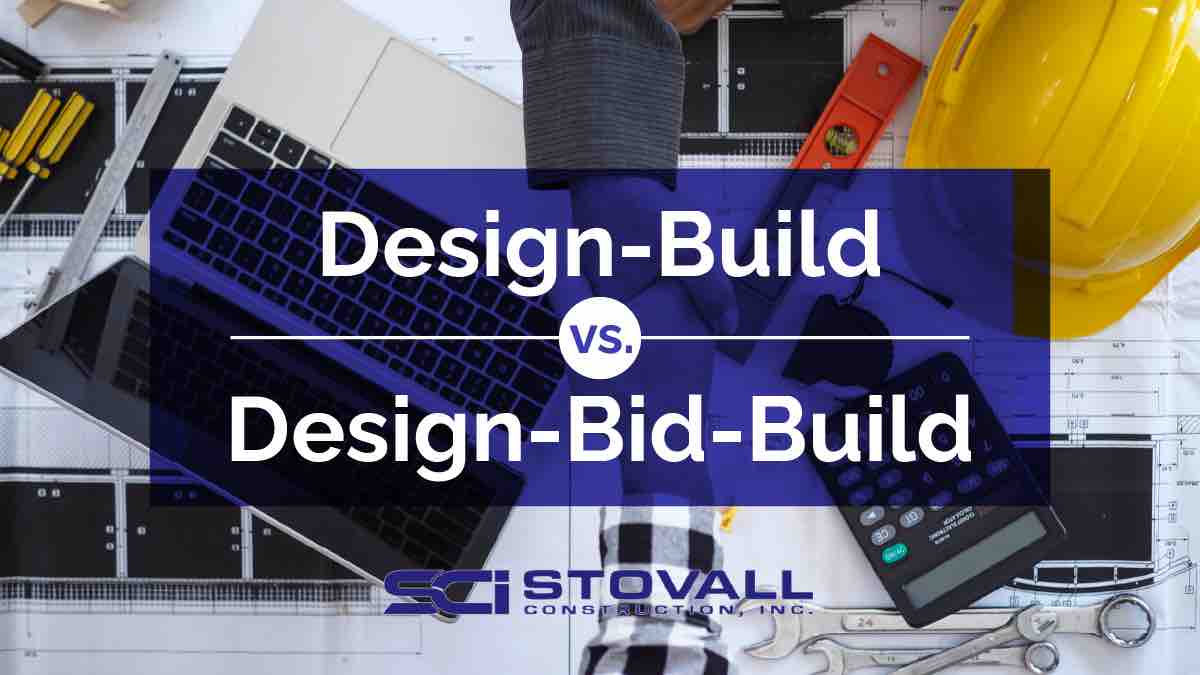
If the agency contracts for development of the scope of work, the procedures in subpart 36.6 shall be used. (2) Data on the agency's past performance, for the prior 3 fiscal years, regarding the time required to definitize equitable adjustments for change orders under construction contracts (see 43.204). If fewer than 3 fiscal years of data are available, agencies shall provide data for the number of fiscal years that are available. Data shall be provided in the solicitation notice as shown in the following table, or provide the address of an agency-specific, publicly accessible website containing this information. An adequate change order definitization proposal shall contain sufficient information to enable the contracting officer to conduct meaningful analyses and audits of the information contained in the proposal. In recent years, the design-build delivery method has been gaining in popularity.
In this series, we’ll examine and compare some of the most widely used project delivery methods, including Design-Build, Construction Manager at Risk and Time and Materials. During the construction phase, the design-builder performs the construction. If you have chosen from a pre-developed set of drawings and the design-builder has experience in constructing from those drawings, you may not need to be too involved in the process. If you have a more custom project, then you would likely be more involved in the development of the design and the construction process. Construction manager at risk (CMAR) is a method of project delivery in which the owner contracts a construction manager to take on a construction project during its design phase, and... The most prominent difference between design-build and design-bid-build processes is the level of interaction between contractors and designers.
Replacing Crumbling 114-Year-Old LaPrele Dam An Urgent Priority - Cowboy State Daily
Replacing Crumbling 114-Year-Old LaPrele Dam An Urgent Priority.
Posted: Thu, 09 Nov 2023 08:00:00 GMT [source]
To minimize this risk as much as possible, project owners can make use of utility mapping in the conception and pre-design phases. The construction phase involves building, inspecting, commissioning, and accepting the project. At the conclusion of the construction phase, engineers need to submit updated utility data that may have changed during the project. Design-build is gaining ground quickly in the construction industry, moving from a new and unfamiliar method to an industry standard. Recent market research from the Design-Build Institute of America (DBIA) anticipated that design-build would represent up to 44 percent of construction spending in 2021, having experienced 18 percent in market growth since 2018. Sectors most likely to choose the design-build method include manufacturing, highway infrastructure, and education.
504 Physical data.
Today she focuses most of her efforts on unlocking the challenges of the subsurface, through research and education. With a proper dispute resolution clause in place, contractors, subs, and suppliers can avoid taking their disputes into litigation. While this method is less collaborative than others, it is still the preferred method for many owners.
The services of designers and builders began to separate after the dawn of the industrial revolution. Because of the complexity of new industrial facilities, design expertise and specialization were required from the designers, but not to the same degree from the builders. The Industrial Revolution also called for dividing the production process into basic, individual tasks. The dramatic difference between the intellectual process of design and the physical act of construction made the design and construction industry easy to separate. With the traditional delivery method, design-bid-build, the primary, if not only, factor considered in the competition is price. The Design-Build selection process, conversely, puts in place a rigorous competition procedure that focuses on qualifications, experience, technical approach, price and other factors.
While DBB doesn't benefit from early contractor input, stakeholders on a DBB project can benefit a great deal from clear, consistent, and organized communication surrounding all aspects of the project's progression. Further, the contractor should maintain open books for the owner to check the current schedule, budget adhesion, and any expected delays. Open communication can go a long way to avoiding or minimizing disputes on a project.
The traditional design bid build delivery method tended to pit one contractor against another in a race to shift blame and responsibility. Siloed information leads to inefficiencies, contrasting opinions, and a combative approach to change management. As mentioned earlier in this post, design-bid-build projects are the most common project delivery method.
During build delivery, the builder or general contractor oversees the construction process, including hiring and managing subcontractors to complete the day-to-day building tasks. The general contractor works to stay on budget and on time with the project since they usually absorb any overages—not the owner. However, if there are any changes to the design, the owner is responsible for any additional costs incurred.
The design-bid-build delivery method is best suited for less complicated, predictable projects with a strict budget and a flexible completion schedule. It is often used for large, public projects and is often the delivery method required by public and municipal entities. Design-build is a contracting approach in which a single entity, the design-builder, assumes responsibility for the design, construction, commissioning, and turnover of a project.
No comments:
Post a Comment